Why PE Pipes are more environmentally friendly than PVC pipes
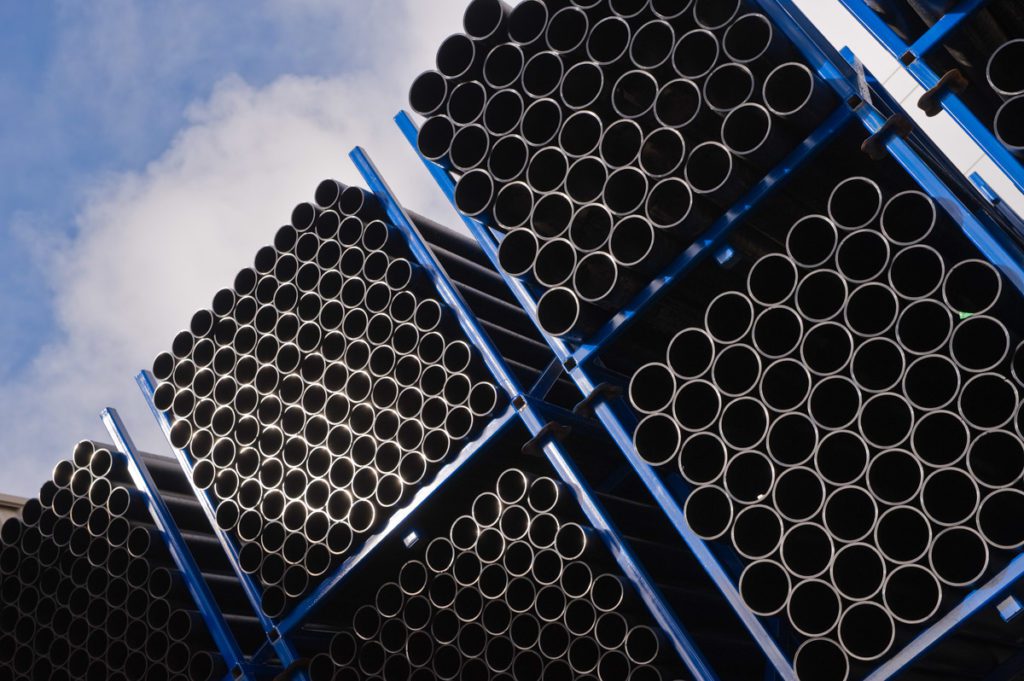
High-density Polyethylene (HDPE) pipes – also known as poly pipes or PE pipes – are quickly becoming known as the most environmentally friendly pipes on the market. They’re an excellent alternative to polyvinyl chloride (PVC) pipes.
HDPE pipe manufacturing began in Australia in the 1950s, but developers didn’t initially create it as a more environmentally friendly alternative to PVC. However, this sustainable, low-cost, and leak-proof alternative to other piping has given HDPE pipes a reputation for sustainability over time.
In fact, Greenpeace now recognises polyethylene and polypropylene as the only “future-friendly” piping materials. Poly pipes have demonstrated a low carbon impact on the environment throughout the product life cycle- from manufacturing to end-of-life.
In this article, you’ll discover why PE(HDPE) pipes are more environmentally friendly than PVC. You’ll also see how Advanced Piping Systems’ poly pipe was used in Australia’s first 6-Star Green Star Rated Office Building. Finally, you’ll find out which industries are driving the demand for this eco-friendly pipe option.
Why PE pipes are more environmentally friendly than PVC
Less leakage
Thanks to the unique heat fusion joining process used during installation, HDPE pipes provide the lowest rate of leakages and the highest guarantee of preserving drinking water quality. They also reduce the possibility of wastewater leakage into the environment, compared to other jointed piping materials that can present excessive sources of leaks at connections.
Less waste in production
According to the Plastics Pipe Institute, the environmental benefits of using HDPE pipes in water and wastewater systems begin with the manufacturing process. “Pipes produced from HDPE resin use significantly less energy to manufacture than other materials such as iron and concrete,” as mentioned in their Position Paper.
In addition, the global production of polyethylene uses less than 1% of the world’s natural gas and crude oil. This is in stark comparison to the manufacturing process of PVC. The Center for Health, Environment and Justice, a non-profit organisation based in New York, calls PVC as “one of the most hazardous consumer products ever created.”
The production of PVC requires a series of chemical reactions. Each step releases waste byproducts that can enter the atmosphere, groundwater, and soil.
“The manufacture of PVC uses a huge amount of nasty, environmentally damaging chemicals,” explains Caleb Craig, Director of Advanced Piping Systems. “A significant amount of the waste by-product from the PVC manufacturing process often ends up back in landfill, often in third-world countries.”
Fewer carbon emissions in transportation
As an incredibly lightweight pipe product, HDPE pipes require far less fuel during transportation to their final location. This means less carbon emissions during transportation compared to other pipe materials, which are much heavier.
Durable and recyclable
Two of the most significant benefits of using polypipe compared to PVC are its durability and recyclability. Advanced Piping Systems’ HDPE pipes have a useful service life of at least 100 years. There is also no need for excavation during service.
When a HDPE pipe does reach the end of its lifespan, there are many opportunities for responsible recycling. “PE pipes can be recycled again and again,” explains Caleb. “Every piece of PE pipe – if it’s in a reasonable condition – will normally go back to the pipe manufacturer for regrinding before being put back into the mix to make more pipe.
“Even very low-grade recycled HDPE pipe is usable, being turned into things like bumpers in car parks.”
For these reasons, the industry is increasingly recognising polypipe as a far more environmentally friendly option than PVC pipe.
Polypipes used in Australia’s first 6-star green-rated office building
The SA Water building in Victoria Square, Adelaide, became Australia’s first commercially developed building to earn a 6-star Green Rating. An Office Design rating from the Green Building Council of Australia.
Completed in 2009, this landmark office building comprises 10 storeys. It provides 12,000 square metres of office space and 5,000 square metres of laboratory space for SA Water over eight floors.
To win this prestigious title, the design, construction, and fit-out of the building followed Environmentally Sustainable Design (ESD) principles. This included installing Advanced Piping Systems’ poly pipe.
“In order for the SA Water building to achieve its 6 Star Green Star rating, it was essential that HDPE pipes, not PVC pipes, were used in construction,” said Caleb.
“We used Advanced Piping Systems’ HDPE pipes throughout the building. This includes the sewer, gas, drainage, potable water, and fire protection.”
Increasing demand for PE Pipes
Australia has used HDPE pipes for over 50 years. But they are now rapidly replacing steel, concrete, and ductile iron piping.
HDPE is the fastest-growing piping material in mining, municipal, industrial, and commercial applications. Experts expect the conversion rate to HDPE to increase by 5% per year.
Caleb believes the environmental benefits are a key reason for the increased demand for PE pipes.
“There’s definitely been an increase in demand for HDPE pipes over the last 15 to 20 years,” he said.
“The environmental benefits of HDPE pipe, when compared to PVC, and its comparable application, mean that HDPE is becoming a more mainstream choice.”
We’re here to help!
Learn more about how we work and discover the Advanced Way. Our friendly customer service team are always ready to answer any questions you may have regarding your next piping project. Give them a call on 1300 362 229 or contact them via the Advanced Piping website today.