Talking shop: a pipefitter’s guide to torque settings
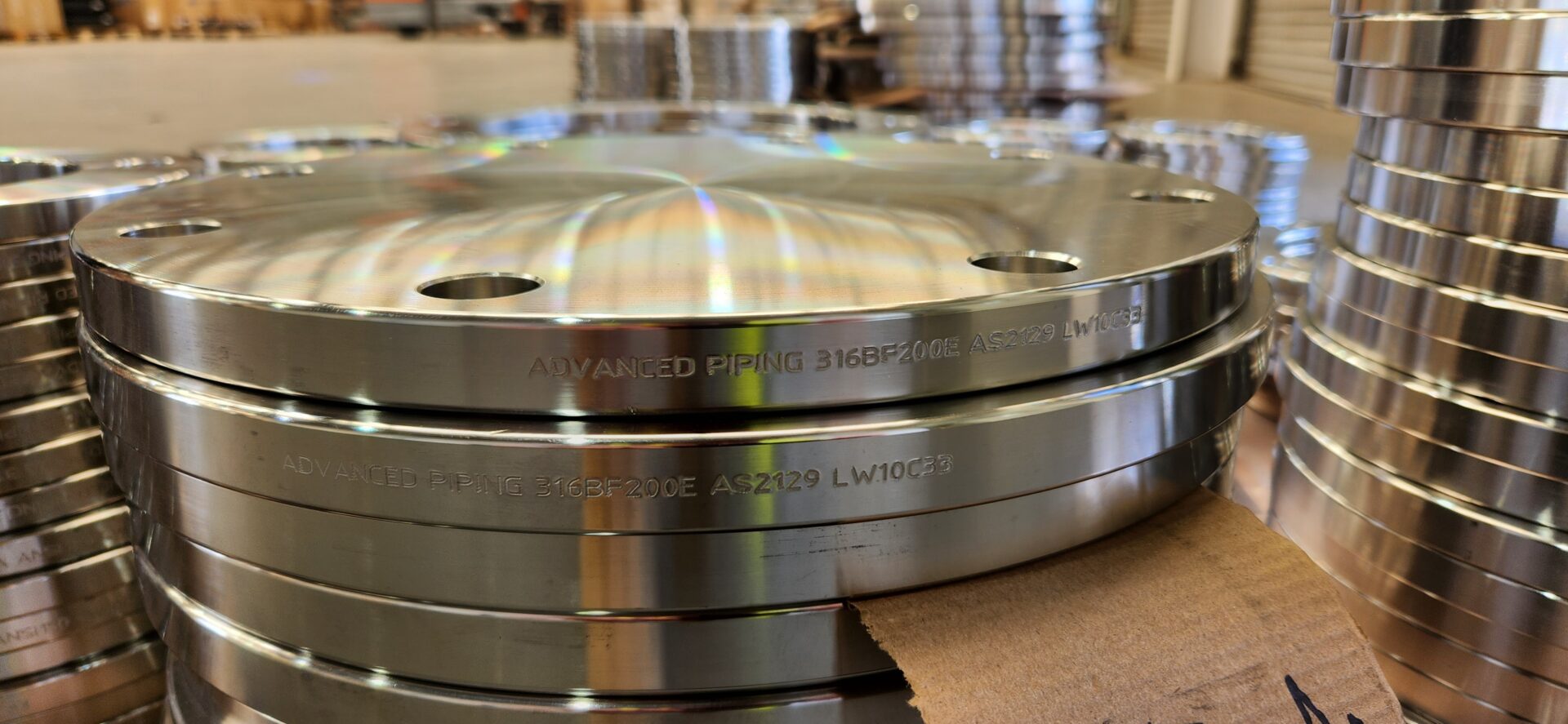
Pipefitters, we need to talk about torque.
Not the type of torque that determines how powerful your ute is (that’s a conversation for another day!)
But torque settings in relation to HDPE pipe. Specifically, how tightly you need to do your bolts up on flanged joints to achieve even pressure on all bolts and avoid leakage.
Knowing which torque setting to use can be challenging — every industry has a different standard, and torque settings vary depending on whether you’re bolting together steel or poly pipe.
Two common issues we see at Advanced Piping Systems include ‘over torquing’ — which occurs when a backing ring is tightened too much — and the application of steel torque settings on poly pipe (and vice versa).
To help you avoid the unwanted consequences of these common mistakes, and understand this complex topic, Nathan Craig, Director at Advanced Piping Systems outlines how to choose the right torque, and our top tips for tightening bolts.
All torque, no action: the problem with over torquing
When over torquing occurs, backing rings become deformed and do not provide a flush connection which leads to leakage, or pipeline failure.
Nathan recently encountered this issue on a mine site.
“The inspector sent us pictures of bent flanges,” he said.
“They first thought there was something wrong with the backing rings, but we had been supplying these same backing rings almost on a weekly basis to the mine site for over 25 years with no issues.
“We suspected that the true cause of issues on site was the over torquing of bolts, not an issue with the product itself.”
It turned out that Nathan’s suspicions were correct. A new installation team had been working on the affected pipe system, and had applied full ANSI 150 torque settings, as if they were bolting steel flange to steel flange.
“This was far too much torque, which was compressing the stub flange, and bending the backing rings,” he said.
“Thankfully, all they needed to do to remedy the situation was just to replace just the flange, which we were able to arrange.”
In order to prevent a major leak, Nathan said it’s important to keep your eye on your backing ring and stub flange while tightening your bolts.
“Whatever torque you select, you need to keep a visual on what’s happening to the backing ring and stub flange,” he said.
“A twisted or bowed backing ring could compromise the strength, and the worst thing that could happen is that the stub flange could pop out, causing a major leak.”
By selecting the right torque settings for your pipe system, you’ll avoid over torquing and ensure the durability and lifespan of your HDPE pipe.
What to consider when choosing the right torque setting for HDPE pipe
The first thing to consider when choosing the right torque settings for your poly pipe system is to identify the material that your gasket is manufactured from.
Different gasket materials — whether rubber/neoprene, fibre, or PTFE — have different properties and compressibility levels, which affect their ability to seal. Essentially, the lower the compressibility rating of your gasket, the higher torque you have to apply.
Rubber (or neoprene) gaskets are good for a range of general applications, including low pressure water and cooling systems. While a rubber gasket does not require a lot of torque to seal due to its compressible nature, it doesn’t have a high pressure rating.
Fibre gaskets are a better choice for higher pressure applications, including transporting gases and liquids. At Advanced Piping Systems, we prefer to use fibre gaskets for two reasons. Firstly, they don’t stretch like insertion rubber gaskets do — when you bolt them up with even torque, they rarely need re-tensioning. Secondly, while fibre may not be as durable as other materials, in our experience, re-fitting is not required.
PTFE gaskets are a good ‘all rounder’, and we tend to recommend them for chemical applications. Being a smooth and hard plastic material, PTFE gaskets require a lot more torque to seal, and are not as forgiving as a fibre or rubber gasket. In some instances, we’ve had to do bolts up so tight we’ve snapped torque wrenches!
The second step for choosing the right torque settings is identifying the pressure class of your poly pipe system. The higher the pressure class, the more torque you need to use.
When you’re working with a high pressure pipe system such as PN20 or PN25 Poly, it’s important that your torque settings are spot on. That’s why at Advanced Piping Systems, when we run pressure tests at 1.25 or 1.5 times the required working pressure, this is a real test for the flange and gasket seal and ensures gas or liquid won’t escape when installed on site.
Top tips for tightening bolts
Once you’ve identified your torque settings, follow these tips to help you achieve even pressure on all bolts.
Use the correct bolts
If your flange requires a M22 bolt, use a M22 bolt. A M16 or M18 bolt — even if it’s done up to the right torque settings — will not pull the flange together with the same force.
Follow a flange bolt-up procedure
To ensure even distribution of stresses and a uniform seal, tighten the bolts to the first torque value in the sequence, using a star pattern, then repeat the star pattern while tightening to the next torque value, and so on up to the maximum torque value.
Make sure you’ve got the right tools for the job
Even torque settings are critical, so we always recommend you use a torque wrench to tighten your bolts. If done by hand, your first few bolts might be tight, but then human fatigue sets in! Even if one or two bolts are tighter than the others, we find the flanges leak.
Use a dry, preferably carbon-based lubricant for the bolts
Torque settings have been determined for lubricated bolts. You’ll need to apply far more clamping force if you don’t use lubricant.
Multiple Pss Bolt Torque | |||||||||
Size
(in) |
Max
Torque |
Torque Sequence (ft-1b, lubed*) |
Torque Sequence (ft-lb, unlubed**) |
||||||
1st | 2nd | 3rd | 4th | 1st | 2nd | 3rd | 4th | ||
2 | 22 | 5 | – | – | – | 5 | 10 | 22 | – |
3 | 30 | 5 | 12 | 15 | – | 15 | 20 | 30 | – |
4 | 30 | 10 | 15 | 20 | – | 15 | 25 | 30 | – |
6 | 44 | 12 | 24 | 30 | – | 20 | 32 | 44 | – |
8 | 58 | 15 | 35 | 40 | – | 30 | 40 | 50 | 58 |
10 | 58 | 25 | 50 | 60 | – | 20 | 40 | 60 | 58 |
12 | 75 | 30 | 60 | 72 | – | 20 | 50 | 65 | 75 |
14 | 140 | 46 | 92 | 126 | 140 | 35 | 70 | 105 | 140 |
16 | 140 | 46 | 92 | 126 | 140 | 35 | 70 | 105 | 140 |
18 | 140 | 46 | 92 | 126 | 140 | 3535 | 70 | 105 | 140 |
20 | 140 | 46 | 92 | 126 | 140 | 40 | 70 | 105 | 140 |
22 | 160 | 53 | 106 | 144 | 160 | 45 | 80 | 120 | 160 |
24 | 180 | 59 | 119 | 162 | 180 | 45 | 90 | 135 | 180 |
26 | 180 | 59 | 119 | 162 | 180 | 45 | 90 | 135 | 180 |
28 | 180 | 59 | 119 | 162 | 180 | 45 | 90 | 135 | 180 |
30 | 180 | 59 | 119 | 162 | 180 | 45 | 90 | 135 | 180 |
32 | 240 | 79 | 158 | 216 | 240 | 60 | 120 | 180 | 240 |
36 | 260 | 86 | 172 | 234 | 260 | 65 | 130 | 195 | 260 |
* Assumes the use of SS, zinc- or cadmium-plated bolt and/or bolt along with copper-graphite anti seize lubricant brushed directly on to the bolt threads.
**Assumes the use of zinc-or cadmium-plated bolt, nut or both. Never use unlubricated, uncoated bolts and nuts with vinyl flanges, as high friction and seizing lead to unpredictable torque and a high incidence of cracking and poor sealing.
Note that the toques listed in the table are for flange-to-flange connections in which the full faces of the flanges are in contact. For other types of connections, such as between a flange and a butterfly valve, where the full face of the flange is not in contact with the mating component, less torque will be required.
Do not apply the maximum listed torque to the bolts in such connections, which may cause deformation or cracking, since the flange is not fully supported by mating component. Instead, start with approximately two-thirds of the listed maximum torque and increase as necessary to make the system leak-free after pressure testing.
Still need a hand understanding torque settings? Advanced Piping Systems’ experienced and qualified sales team know what they’re talking about! Contact us today to find out how we can help.