Managing the impact of China’s disrupted supply chain
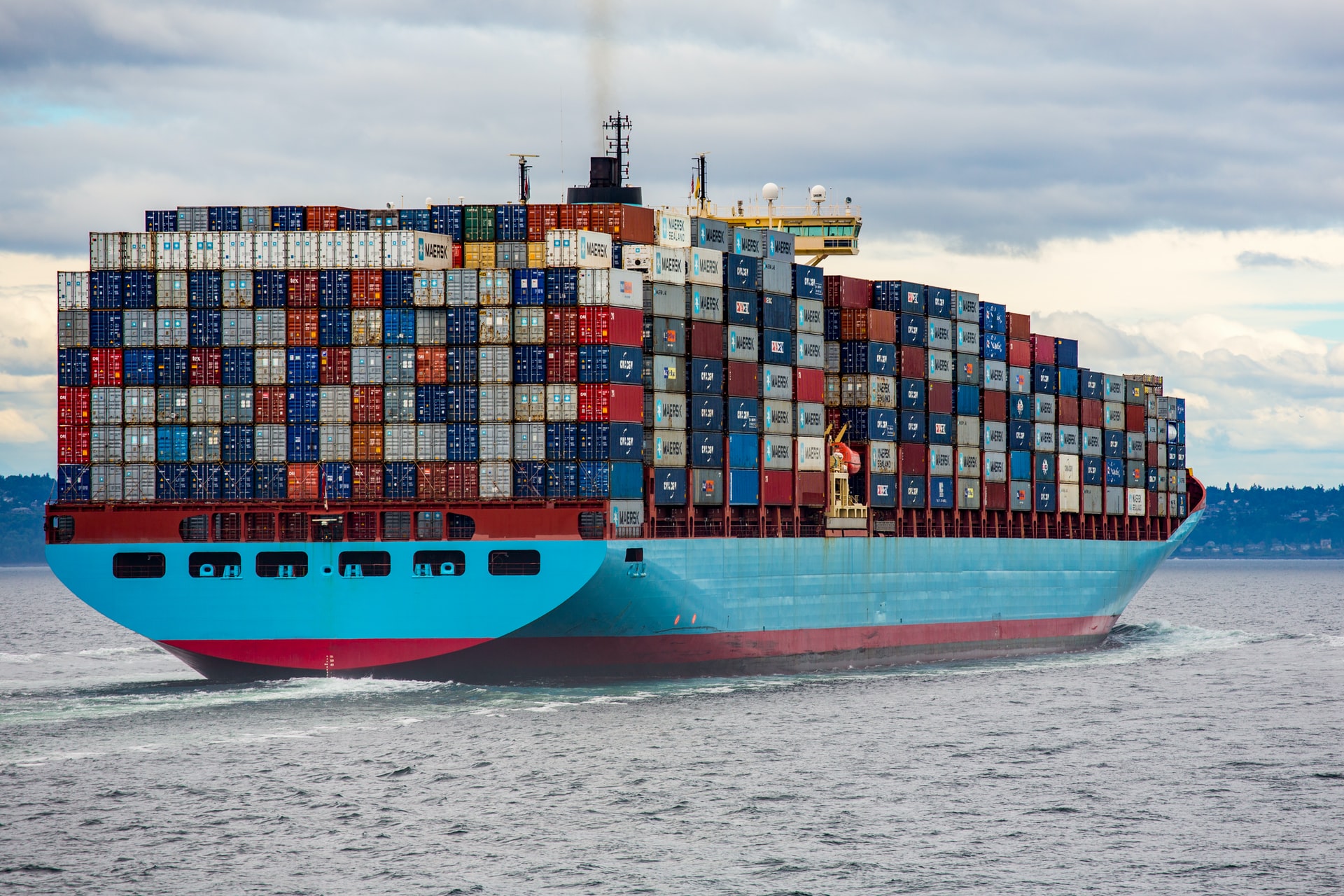
From isolation to one of the world’s greatest economic powers, China has undergone a remarkable transformation in the past 70 years.
As the world’s second largest economy and the leading provider of manufacturing services, China’s cheap labour and construction materials are now in high demand from Australia.
But in the wake of the COVID-19 pandemic, many of our largest infrastructure and mining projects requiring HDPE pipework are at the mercy of China’s disrupted supply chains, and as a result, are paying the price for years of low-cost materials.
With Chinese manufacturers, suppliers, exporters and the shipping lines, airlines, non-vessel operated cargo-carriers, freight forwarders and other intermediaries struggling to deliver goods, organisations which depended on China to fulfil their need for raw poly pipe materials or finished products have become exceptionally vulnerable.
As each day passes, there are countless mine sites, processing plants and infrastructure projects across Australia facing hundreds of thousands of dollars of liquidated damages and losses in production due to delays.
And there’s no end in sight.
At Advanced Piping Systems, we’ve been contacted by project managers and engineers across the country who are facing costly delays on their projects, and now need a guaranteed, ‘quick-fix’ solution to resume work.
If you’re in this position, or want to avoid it altogether, Director of Advanced Piping Systems, Caleb Craig, explains why it always pays to consider more than just price when specifying materials for a job — and the benefits of engaging a supplier in your own backyard.
Understanding China’s disrupted supply chain
In the past decade, large Australian engineering companies and projects have been increasingly sourcing and manufacturing HDPE materials, prefabricated work, and modular systems from China, which are shipped across in sections before being bolted together on site.
Offering competitive pricing thanks to its significant labour force and production facilities, the demand for Chinese materials has never been higher.
But recent issues with China’s steel production and electricity supply, coupled with the COVID-19 pandemic, has led to significant disruptions in the supply chain — including soaring raw material costs, long delays at ports and shortages of shipping containers.
“What’s happened since COVID-19 is that there’s been a massive spike in demand, thanks to economic stimulus spending worldwide on infrastructure and housing,” Caleb said.
“But while demand for Chinese materials has never been higher, China itself has been experiencing major issues with their own steel production and electricity supply, which has shut down whole industry sectors.
“Because of this, there’s less labour available, and materials — steel in particular — are getting very lean.
“Recently, we’ve also heard of a lot of quality issues with HDPE being produced in China.”
These shortages have led to significant delays and increases in shipping costs.
“What used to be a very quick shipping line between Australia and China has now been extended significantly due to hold ups in ports in Singapore,” Caleb said.
“Sea freight is currently only about 10 percent predictable, where it used to be 80 or 90 per cent predictable.
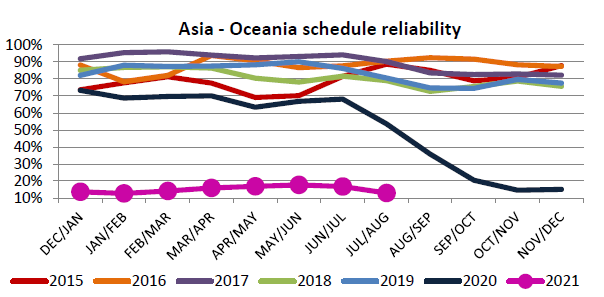
“For an industry that is driven by time and deadlines, it’s devastating.
“This has dramatically increased shipping costs which are through the roof — about four times higher than what you would have paid a few years’ ago.”
Disrupted supply chains = disrupted projects
Unfortunately, many suppliers and importers have not acted fast enough to soften the blow of China’s disrupted supply chain, with their end customers often naive to the reality of the situation.
“Importers of finished, prefabricated or engineering structures have felt this for months and months now, but unfortunately, many didn’t move quickly enough to find alternate solutions,” Caleb said.
“There’s a lot of naivety from a customer perspective, as suppliers didn’t want to put uncertainty in their supply chain.
“They’ve really shielded the reality from their customers.”
These customers are now reaching out to Advanced Piping Systems, having realised the full impact of the delays on their projects and looking for a ‘back-up’ plan.
“One project company subcontracted some prefabricated pipe skids to China six to 12 months ago, expecting a delivery deadline of January 2022,” Caleb said. “But they’ve just received an update that they won’t be receiving their order until March.
“Of course, that doesn’t come with a guarantee — with the shipping lines in the state they are, who knows what will happen.”
These delays are coming at a huge cost to both the engineering company and end user, through liquidated damages and loss of production.
“A minimum three-month delay that could be extended for even longer is a huge risk and unknown, and you don’t even know what it’s going to cost, with raw materials fluctuating in price so much,” he said.
Why it pays to consider more than just price
This example is just one of many that highlights why now more than ever, it is important to consider more than just price when specifying and sourcing HDPE pipework.
Guaranteed quality, stock levels, delivery dates and knowing you’ve got a trustworthy supplier on your side are all benefits to sourcing materials locally.
“There are significant benefits of sourcing from an Australian company, like Advanced Piping Systems,” Caleb said.
“We stock a large quantity of materials, so if you place an order with us, we know exactly what the lead time will be to produce an item, and the exact cost for the complete package. In fact, we 100 per cent guarantee our lead times.
“You also have peace of mind knowing you’re receiving a quality product – it’ll be Australian made to Australian standards.
“And there’s probably going to be less assembly when it gets to site, because we haven’t had to disassemble the package in order to transport it.”
How to avoid costly delays on your project
While many companies have learnt the hard way, by being sure of your supplier’s supply chain, and sourcing locally, you can avoid costly delays on your pipework project.
If you’re about to start a new pipe project, Caleb advises buying local from the get-go.
“For those who are starting a new project, my advice is to buy local.
“Make sure your materials are coming from a local supply chain or a guaranteed shipping solution.”
If you’re currently waiting on products to arrive from China or experiencing delays, your best bet is to undertake a cost-benefit analysis.
“My advice would be to really consider your costs,” Caleb said.
“If you’re being told there’s going to be a three-month delay, work out the actual cost of that delay on your project in terms of liquidated damages.
“Based on this figure, it might be worth cutting your losses — it’s highly likely that the situation in China will only get worse, meaning you could be up for another six months of liquidated damages.”
And if you’ve ordered products from China that are still waiting to be shipped – it’s not too late to jump ship.
“If your product hasn’t left China, I’d advise pulling pins or running with a local supplier, that can guarantee a deadline.”
Advanced Piping Systems, Australia’s number one PE pipe and fittings specialist
At Advanced Piping Systems, we predicted that global supply chains would be put under immense pressure 18 months ago, and strengthened our supply accordingly.
With supply chains expected to be out of action for at least the next six months’, if your project is facing lengthy and costly delays, we are here to help.
Contact our customer service team today or request a quote to get your project back on track.