Advanced Piping Systems’ precision HDPE spooling future-proofs iron ore mine
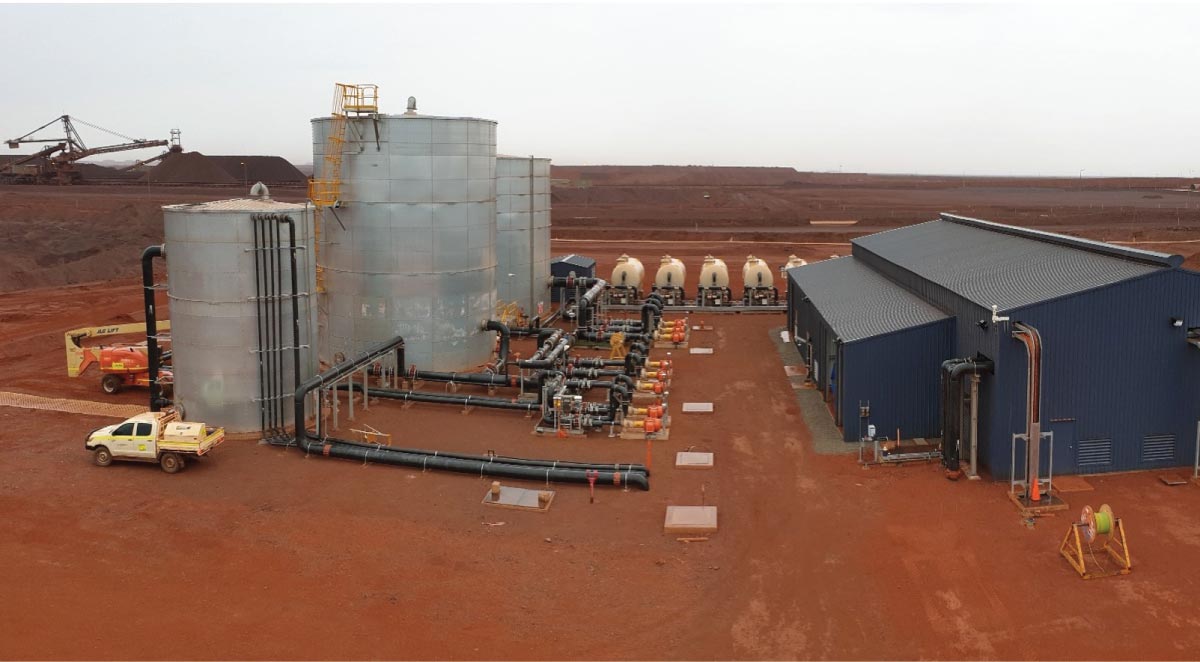
In 2022, Advanced Piping Systems supplied HDPE spooling and pipe to an A$100 million water management upgrade project. This was at an iron ore mine in the Pilbara region of Western Australia.
Working in partnership with a leading national multidisciplinary industrial services provider and a leading national water and waste treatment provider, the project would increase the capacity of the mine’s reverse osmosis (RO) plant from 10 mega litres to 40 mega litres. Future-proofing its operations for the next 20 years.
As part of the RO plant’s upgrade, we were required to first deliver precision poly pipe spooling for the plant before supplying the interconnecting HDPE piping to connect the new RO plant to the mining infrastructure.
Our Business Development Manager (SA/NT), Paul Narancic, shares how the team successfully delivered the project despite many challenges.
Rising to the challenge
The project was split into two stages. The first stage, completed in 2018, involved treating brackish water. While the second stage, completed last year, saw the plant increase its capacity.
“Ore from the mine must be washed to remove chloride-based salts before shipments, which requires a huge amount of water,” Paul said.
“Stage 1 involved constructing a 10 megalitre plant to treat the ‘brackish’ water, which is salty, but not as salty as seawater.
“As the mine ages, the feed of water into the system becomes saltier, so in Stage 2, a much larger RO plant was built to increase the mine’s water processing capacity from 10 to 40 mega litres.
“This increase ensured a plentiful supply of clean water for processing over the life of the mine.”
Advanced Piping Systems was selected for this job thanks to our fabrication capability, willing workforce, and adaptability. Our digital QA systems and network of global suppliers also played a crucial role.
“There was a complexity to the project, which required our experience and an in-depth knowledge of HDPE systems,” Paul said.
“When our competition said ‘no’, we said ‘yes’…we made a commitment to deliver — and we did exactly that.”
Delivering on our word
According to Paul, the project presented many challenges. This included exceedingly tight timelines, maintaining spool accuracy from isometric drawings, temperature deflection, and distance to the site.
“These spools required far greater accuracy than the Australian Standards suggest, so there was a big challenge using isometric drawings to supply accurate piping to a project 3,300 kilometres away,” he said.
“The plant spools were fabricated with high accuracy because they were required to be installed in a purpose built modular framework.
“To take into account temperature deflection, we suggested additional breakpoints to allow for greater adjustment on site.
“We also added “green” pipe to the spools for the interconnecting section, so they could be cut and adjusted on site to suit changes from the original iso drawing.”
Advanced Piping Systems put on double labour shifts, weekend work, and a constant stream of trucks moving through the yard to meet the tight deadlines for the interconnecting section. There was also extra staff to assist our designated full-time project management resources and ensure the project’s success.
Advanced Piping Systems conducted weekly video updates to overcome the distance to the site. We also flew to Perth for face-to-face project updates during the fabrication process. Additionally, we developed an online spool tracker, which meant each spool could be tracked through the production process with an ETA.
All in all, the team delivered more than 1,500 spools, supplied pipe ranging from 900mm to 1200mm and 7,500 fittings, and spent over 5,000 hours working on the project. That’s a huge effort from everyone involved!
If you need a reliable HDPE fabricator and supplier, Contact our knowledgeable Customer Service team today.